Water risk on HFDU hydraulic fluids. How to minimize the impact?
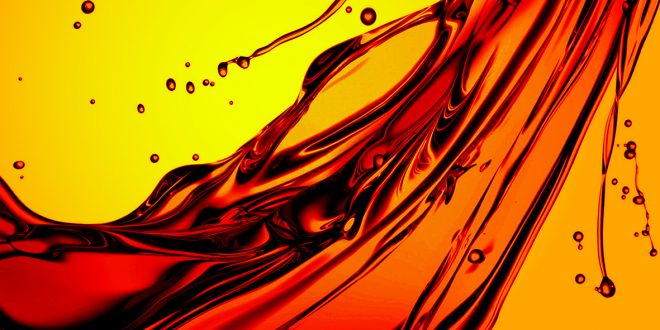
For more than 25 years, CONDAT has been designing lubricants dedicated to the steel & aluminum industries: high performance technical greases & fire-resistant hydraulic fluids.
CONDAT ambition is to offer the most efficient solutions to both increase its customer productivity and reduce energy & resources consumption. This is what we called Responsible Performance.
CONDAT lubricants technologies, CONDAT MILLENIUM greases & CONDAT D fluids meet this target thanks to a very high level of performance.
To go beyond the plain commercial claim, CONDAT has solicited an independent laboratory to conduct test on its CONDAT D range. Find out in this article how the hydrolysis resistance can affect product performance of fire-resistant oils. Scientific evidence to follow!
CONTEXT:
WATER, A MAIN ISSUE FOR STEEL & ALUMINUM WORKSHOP MANAGERS
All workshop managers are looking to minimize their maintenance costs and want to optimize the life time of their lubricants batch. Indeed, huge quantity of hydraulic oils are at stake as a tank can reach 2 000 to 10 000 liters. One option to increase drain intervals is to follow up carefully the pollution of the fluid in order to increase its operating lifetime.
In workshops, the phenomenon of condensation may be important. It is mainly due to the temperature difference between hot point on the circuit and the tank or the outside humidity entering the circuit through the air filtered from outside by the air filter… Ester based HFDU fluids are known to be sensitive to water who plays a major role in the degradation of the fluid and hence on its operating lifetime.
In order to follow as closely as possible the water content and to minimize draining, CONDAT advises to regularly analyze the fluids in service. It should be done at least once a year in order to control the water content and other pollutions. However, the most effective way to reduce water impacts on the operating lifetime of the fluid is to design water resistant products.
Objective: keep the fluid in service under good conditions as long as possible to save on the lubricants purchase budget!
HYDROLYSIS OR HOW WATER IMPACTS ESTERS
To put it simply, the water will react with the ester to form an acid.
The acid is a more reactive molecule and with high temperature and oxygen, the acid molecules will start to react with the ester molecules. Once initiated, a chain reaction will take place, the ester-based molecules will be broken and highly instable, they will react with each other, creating bonds between different molecules and generating acidic by-products.
Looking at an analysis results sheet, this will translate by an increase in the viscosity, in the Total Acid Number* (measuring the acids in the fluid). These acidic components will tend to dissolve in the water phase and decrease its pH. They will also tend to be more aggressive to metal, maybe creating corrosion.
Hydraulic fluids that are unstable to hydrolysis form acidic and insoluble contaminants which can cause hydraulic system malfunctions due to corrosion, valve sticking, or change in the viscosity of the fluid.
MESURING CONDAT D RESISTANCE TO WATER
CONDAT recently commissioned an independent laboratory to obtain an impartial opinion on the hydrolysis resistance of its CONDAT D fluids. The laboratory was asked to measure the resistance to hydrolysis and oxidation on CONDAT D68 and 2 equivalent products from the market.
The test method ASTM D2619 (see opposite) differentiates the relative stability of hydraulic fluids in the presence of water under relatively high temperature and the presence of a copper acting as a catalyst to initiate the oxidation reaction.
Here the results of the independent laboratory:
Test method description
(ASTM D2619)
75 g of sample is mixed with 25g of water and along with a copper test specimen and are sealed in a pressure type beverage bottle. The bottle is rotated, end for end, for 48h in an oven at 93°C.
Layers are separated and insolubles are weighed. Weight change in copper is measured. Viscosity and acid number changes of fluid and acidity of water layer are determined.
*TAN (Total Acid Number, expressed in mg KOH/g) measures the fluid acidity which is related to the oxidation level of the fluid.
Graphs here above (TAN Difference and Water acidity) show how important is the choice of the esters.
Competitor 2 is an HFDU based on natural based esters: After only 48h, TAN variation and acidity of the free water is significantly higher showing that the hydrolysis process has already started to degrade the fluid. This means that more acidic compounds were created by the hydrolysis attack of the water on the esters. Those acidic compounds will create an instability and will fasten the oxidation process.
But even with synthetic ester-based fluid, Competitor 1 and CONDAT D68 behave very differently meaning that the choice and selection of the raw materials is of prime importance. And this only after 48 h of test!
After a few weeks, months, the hydrolysis process will lead to viscosity increase, meaning that the initial setting done for a viscosity of 68 cSt will no longer be valid. Standards accept a ± 10% in viscosity change (74.8 cSt is the upper limit). If viscosity change is too important (over 10%), cavitation may occur leading to a lack of lubrication. This can impact the overall performance & productivity of the system and can damage the hydraulic parts fed by the hydraulic oils.
Damage can also be created by an increased corrosion as the water gets more acidic as the photo below is showing. Condat D68 is less affected by corrosion.
Overall, this is important for workshop managers in steel & aluminum industries to regularly control the water content of their fire-resistant hydraulic fluids in order not to damage their equipment and keep their level of productivity. The use of a fluid that can resist to water damages and that show high hydrolysis resistance can help a lot in this task.
ZOOM ON CONDAT D FORMULATION
The good results of CONDAT D fluid to hydrolysis resistance can be explained by the high-quality level of the product formulation. CONDAT has very stringent requirements regarding the quality & the type of the synthetic esters used in CONDAT D formulations.
Other characteristics besides the hydrolysis resistance are important for the product success, such as high flash point (also depending on the quality of the synthetic esters), high additivation level to offer excellent anti-wear behavior and equipment protection.
If you get a better viscosity stability during the product lifetime and a better TAN evolution, it means:
- A consistant lubricity during temperature changes
- A higher oxydation resistance
- A longer life of the product in use: overall, CONDAT D products last 30% longer than some market references.
Conclusion
Through a premium fire resistant hydraulic fluid, CONDAT offers the possibility to steel & aluminum industries operators to make savings on their lubrication budget & maintenance costs. Besides high quality products, CONDAT provides support and expertise, though lubricant analysis follow-up and interpretation, installation audit and counselling.
CONDAT also offers complementary services in order to take all preventive actions that will save you time and money. Looking for strong partnership with its customers but also with steel & aluminum main actors and OEM, CONDAT philosophy is based on 4 points:
- Safety for people and equipment
- Longevity and protection of the machines
- Optimized maintenance costs
- Respect of workers and the environment with biodegradable and nontoxic lubricants
To know more, contact us
Author:
Severine BOURGEOIS
Expert Marketing Product
Chemical engineer, Séverine has been working for Condat since 2003. As Expert Marketing Product, she has high-level expertise in the lubricant field, especially in maintenance oils and high-tech hydraulic fluids. Her mission is to adapt Condat lubricants’ offer to the specificities and needs of industries working under high temperatures conditions such as steel, aluminum, or insulation applications.